 |
|
Форсировка минских двигателей "Поджатый стандарт"
|
|
|
По многочисленным просьбам постоянных посетителей нашего сайта, публикую материал про форсировку минских двигателей. Надеюсь, что в ней Вы сможете найти немало полезных советов для доводки двигателя своего мотоцикла.
С уважением, Nэо
     Для многих мотоциклистов "Минск" стал "школьной партой". Немалое число этих мотоциклов в относительно живом еще состоянии попросту брошены в гаражах и сараях. Однако и они еще могут послужить, например, идеальным объектом для приобретения навыков и отработки различных технических решений.
     Сегодня своим опытом доводки минского двигателя делится Владимир Тураев – картингист и мотокроссмен из Павлограда. Его вариант интересен, в первую очередь, своей доступностью. Разумеется, не следует ждать от мотора слишком многого – в лучшем случае он отдаст 15 л.с. Но при этом он станет экономичнее, а, может быть, даже и долговечнее(за счет тщательности выполнения работ).
     Еще один плюс предлагаемого пути – возможность" частичной" доработки двигателя, соразмерно своим силам и возможностям. Естественно, что и результаты тоже будут частичными. Обратите внимание на то, что работы по цилиндру или должны быть выполнены полностью, или не должны начинаться вовсе; аналогичные ситуации с головкой цилиндра и с парой коленвал – картер. Кроме того, не стоит возиться с коленвалом, если предварительно не доведен цилиндр. И последнее, что следует помнить, - успех работы пропорционален тщательности её выполнения. Небрежность может легко перечеркнуть все труды. Не пренебрегайте предупреждениями, относитесь к делу внимательно!
     Перефразируя Гоголя, можно сказать: "И какой же русский (читай – белорус, украинец, казах и т.д.) не любит мощный мотор!" Предлагаю Вашему вниманию мой вариант "поджатого стандарта". Это минский двигатель с минимальными переделками родных деталей.
Рис. 1 Для работы понадобится бормашина "Гном" с набором фрез-шарошек и абразивных камней.
Рис. 2 В верхнем продувочном окне хорошо виден выступ рубашки цилиндра, который нужно удалить.
Рис. 3 Продувочный канал: 1-верзняя кромка верхнего пропускного окна; 2-касательная к поршню; 3-поршень; 4-верхняя кромка нижнего пропускного окна. Стрелками указано направление продувочной струи.
Сделать "крутой" мотор на коленке, мягко говоря, сложно, поэтому приготовьтесь к применению и станков, и приспособлений, и самое главное – смекалки и слесарных навыков. Ибо доводка двигателей – дело, граничащее с искусством.
Для начала определимся с его состоянием. Если он новый и обкатанный – отлично! Если он старый, тоже ничего – затяните поясок, приобретите коленвал, поршень с кольцами, подшипники и манжеты.
Цилиндр
     Гильза минского мотора залита в рубашку и провернуть её или выпрессовать невозможно, поэтому добиваться совпадения окон в гильзе с каналами в рубашке цилиндра следует снятием металла. Помните, что толщина стенок рубашки цилиндра и горловины картера должна оставаться не менее 3 мм.
     Обработка каналов – довольно трудоемкий процесс, а облегчить его позволят бормашина с набором фрез-шарошек, абразивных шарошек и различные шаберы (плоский, трехгранный) (рис.1)
     Конечная цель доработки продувочных каналов – добиться их симметричности и высокой частоты поверхности. Полировать каналы не обязательно, однако поверхность их должна быть гладкой как на вид, так и на ощупь. Помните, не следует изменять высоту верхних пропускных окон – это может ухудшить характеристику двигателя, если соответственно не изменять и другие окна. Кроме верхних окон, в пропускных каналах следует оставить неизменным и вертикальным угол продувки (рис. 3).
     Моя методика измерения углов такова.
Рис. 4 Определение вертикального угла продувки при помощи "клюшки".
Из мягкой проволочки диаметром 2…3 мм делаем "клюшку" с изогнутым почти под прямым углом кончиком длиной 10…12 мм и, вкладывая этот кончик в продувочный канал, добиваюсь прилегания "клюшки" как к "потолку" канала, так и к зеркалу цилиндра (рис. 4). Горизонтальные углы продувки определяют опять же "клюшкой", но на этот раз прикладывают её к боковым стенкам канала, а загнутый кончик указывает место выхода канала на заднюю стенку гильзы.
     (В действительности потребуется набор клюшек разной длины - ред)
     Величина "А" (рис. 5) смещения вершины угла от продольной оси гильзы колеблется от 0 до 10 мм и должна быть одинакова для обоих каналов.
Рис. 5 Рабочая схема доводки продувки: 1-продувочный канал; 2-рубашка цилиндра; 3-гильза цилиндра.
     Величина "В" (рис. 5) – расстояние от кромки выпускного окна до передней кромки перепускного окна тоже является одной из величин контроля симметрии каналов.
     Передняя кромка перепускного окна должна быть острой (см. рис. 5, выноска 1), чтобы продувочная струя "отрывалась" от стенки канала без завихрений. Нижнюю кромку верхнего продувочного окна следует опилить по радиусу, примерно равному толщине гильзы так, чтобы продувочная струя была касательна к поверхности поршня в точке отрыва от окна (рис. 3).
Верхнюю кромку нижнего перепускного окна тоже следует опилить по радиусу (рис. 3).
Рис. 6 Дополнительное центрирование цилиндра шпилькой: 1-гильза цилиндра; 2-рубашка цилиндра; 3-шпилька; 4-центрирующий буртик; 5-картер.
     Ввиду того, что отверстия в рубашке цилиндра значительно больше диаметра шпилек, возможно смещение, а значит, и несовпадение перепускных каналов по привалочной плоскости цилиндра. Для обеспечения однозначной сборки изготавливается шпилька с центрирующим буртиком (рис. 6). Материал шпильки – сталь 20. Проверьте, свободно ли входит юбка цилиндра в собранный без прокладки картер. Если нет – снимите шабером лишний металл в горловине картера. Гильза должна входить без натяга. Теперь можно подгонять рубашку цилиндра по центрирующей шпильке.
     Перепускные каналы по разъему "рубашка-картер" подгоняются с помощью шаблона, повторяющего контур перепускных каналов рубашки.
     Юбка гильзы ни в коем случае не должна перекрывать перепускные каналы. При наличии перемычки её удаляют и подгоняют окна в гильзе соответственно окнам в картере.
     В отличие от перепускных, выпускное окно можно немного "распилить", но лишь для того, чтобы выровнять поверхность. Важно, чтобы был плавный, без ступенек переход от круглого диффузора к прямоугольному, с закруглениями, выпускному окну.
Рис. 7 Выпускное окно. Тонкой линией указана форма старого окна. Размер 60 мм указан от верхнего торца цилиндра.
Рис. 9 Доработка поршневого кольца.|
Рис. 8 Фаски для облегчения работы колец.
     Выпускной канал необходимо не только хорошо выровнять, но и обязательно отполировать, что позволит до минимума снизить торможение газа на выпуске. При подпиливании верхней и нижней кромок окна можно придать ему овальную форму (рис. 7). Фаски (рис. 8) как на выпускном, так и на верхней перепускных окнах смягчают переходом поршневых колец через их поперечные кромки.
     С поршневых колец тоже следует снять фаски (рис. 9), желательно на алмазном круге, так как он обеспечивает малую шероховатость. Кольца следует покрыть матовым хромом толщиной 50…80 микрон (мкм). Зазор в замке кольца должен остаться прежним – подпилите его до 0,2…0,3 мм.
     Поверхность гильзы цилиндра обрабатывается шлифовкой, хонингованием или притиркой. Шероховатость поверхности Ra 0,32, отклонением от цилиндричности до 0,01 мм. Зазор между юбкой поршня и зеркалом цилиндра 0,04…0,05 мм измеряется достаточно точно при помощи набору щупов.
Поршень
     Окна в юбке поршня должны соответствовать окнам в
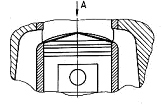 Рис. 10 Согласование формы днища поршня с продувкой. Выделенную жирной линией часть поршня удалить.
юбке гильзы. Все кромки на юбке поршня радиусом 0,5 мм. В нижней мертвой точке поршень не должен закрывать нижнюю кромку верхнего перепускного окна. В противном случае
Рис. 11 Поршень в сборе с шатуном: 1-стопорное кольцо; 2-поршень; 3-палец; 4-шайба; 5-сепаратор; 6-шатун; 7-ролик.
либо снимаются лыски (рис. 10), либо протачивается головка поршня по радиусу 70 мм на необходимую величину. Днище поршня после проточки должно быть не тоньше 5 мм. Поскольку шатун центрируется по цилиндру, торцы бобышек обработайте на фрезерном станке (рис. 11). Размер "А" для обеих бобышек не должен отличаться более чем на 0,1 мм. Шайбы поз. 4 изготавливаются из стали 40X, калятся до твердости 45…50 по НРСа и шлифуются с торцов.
     Поршневой палец облегчается проточками на конус (см. рис. 11). Длина внутренней цилиндрической части должна быть на 2…3 мм больше длины роликов верхнего игольчатого подшипника. Толщина стенки с торцов пальца – 1…1,5 мм. При доработке пальца берегите его рабочую поверхность от повреждений.
Окончание статьи: скоро
Статья из журнала МОТО №8/94
Статью прислал: Zerios
Обсудить статью в Форуме
|
|
DMV studio
Copyright © 2004 |
|
|
 |
| |